

- Cnc usb controller setup drivers#
- Cnc usb controller setup manual#
- Cnc usb controller setup software#
- Cnc usb controller setup Pc#
- Cnc usb controller setup license#
The voltage output pins are between AVI and ACM ground screw terminals. There is a seperate available 10 volt PWM that can be used to control spindle speed. The PWM can also be configured as active low or active high. The output ports are Open Drain/Collector type, a pull up resistor may be required. Below are the oscilloscope images of 3k rpm, 12k rpm and 23k rpm spindle output speeds. The optocouplers have been tested and worked fine with a supply voltage up 24 volts. A minimum of 5.5 volts is required to activate the optocouplers. This requires a separate power supply connected to screw terminals labeled 24V and DCM ground. The I/O ports have E元57N optocouplers for safety. This can be limit switches, ESTOP, PWM, touch probe etc. These input and output ports can be configured as needed for the various functions that MACH3 supports. There are also four input and four output ports. There is no ENABLE output on this controller board
Cnc usb controller setup drivers#
Since the board uses a line driver for the step and direction outputs, the connection to stepper drivers is simple. The step and direction signals can be configured as active low or active high in MACH3 ports and pins setup page. This step pulse width is long enough to work with almost every stepper driver available. When the plugin driver is set at 100Khz, the step pulse width is 5 microseconds. I verified this with both short and extra long motion moves. The correct number of step pulses was generated for each commanded motion distance. I used a logic analyzer to capture and count the step pulses. The step and directions signals are buffered with a 74HC541 line driver. The controller has four step and direction axis output ports – X, Y, Z and A. Slave axis configuration has been tested, the same step pulse was generated on both the X and A axis outputs simultaneously. Step frequencies below 50Khz are better and motor motion is smoother. These pauses can cause rough motor motion. However at higher step frequencies, there are pauses in the step pulse train.

Cnc usb controller setup Pc#
Using a microcontroller to generate step pulses is usually more reliable than a PC parallel port. Save the Mach3Mill.xml file in your Mach3 root folder.The controller uses a STM32F103 microcontroller to generate the step pulses up to 100Khz. Step 5: Download the XML Mach3 Config File above by right clicking on the link and selecting ""save as"". This will allow your board to communicate with Mach3. Select the ""RnRMotionController"" and check ""Don't ask me again"". Step 4: Open Mach3 and you should be prompted to select a driver. It should automatically recognize the USB device. Step 3: Make sure you board is connected to the PC via USB cable. Step 2: Download the USB Motion Driver RnRMotion.dll from the link above and copy and paste the file into your Mach3 Plugins folder Example: ""C:/Users/ProgramFiles/Mach3/Plugins"" If you already have a licensed copy of Mach3 skip this step.
Cnc usb controller setup license#
Step 1: Installing Mach3: You will need to purchase a Mach3 license and download the software. Mach3 Configuration File RIGHT CLICK AND SELECT ""SAVE AS""
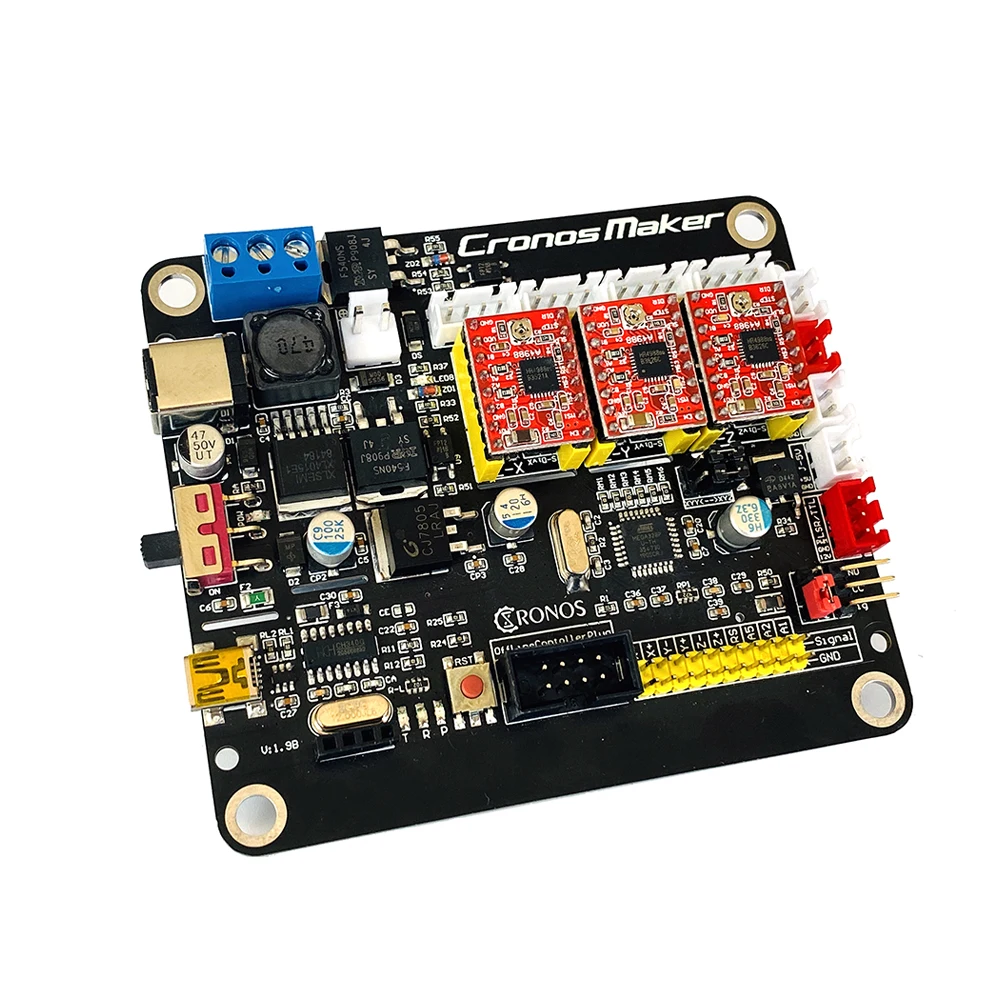
Cnc usb controller setup manual#
Manual and Driver Downloads Click On Links to Download or View 1 status LED indicate connection status on the board.4 general-purpose isolated relay drive output interface can drive four relays for controlling the spindle starts forward rotating and reverse rotating pumps and other device.4 general-purpose inputs you can connect the limit switch estop switch probe switch back to zero and other device.
Cnc usb controller setup software#

Need use external 24V DC power supply to isolate USB and external port and to make the system more stable.Support for connecting electronic handwheel.Maximum step-pulse frequency is 100KHz which is suitable for the servo or stepping motor.Support for 4-axis linkage you can connect four stepper motor drives or servo drives.CNC USB MACH3 100Khz Breakout Board 4 Axis Interface Driver Motion Controller Features: The card can run what all other MACH 3 controllers can run and supports the drive shaft and the driven shaft gantry supports automatic leveling and has an output pulse 100 KHz. This 4 Axis CNC USB Controller is designed to be used for notebook and tablets simple configuration and compatibility.
